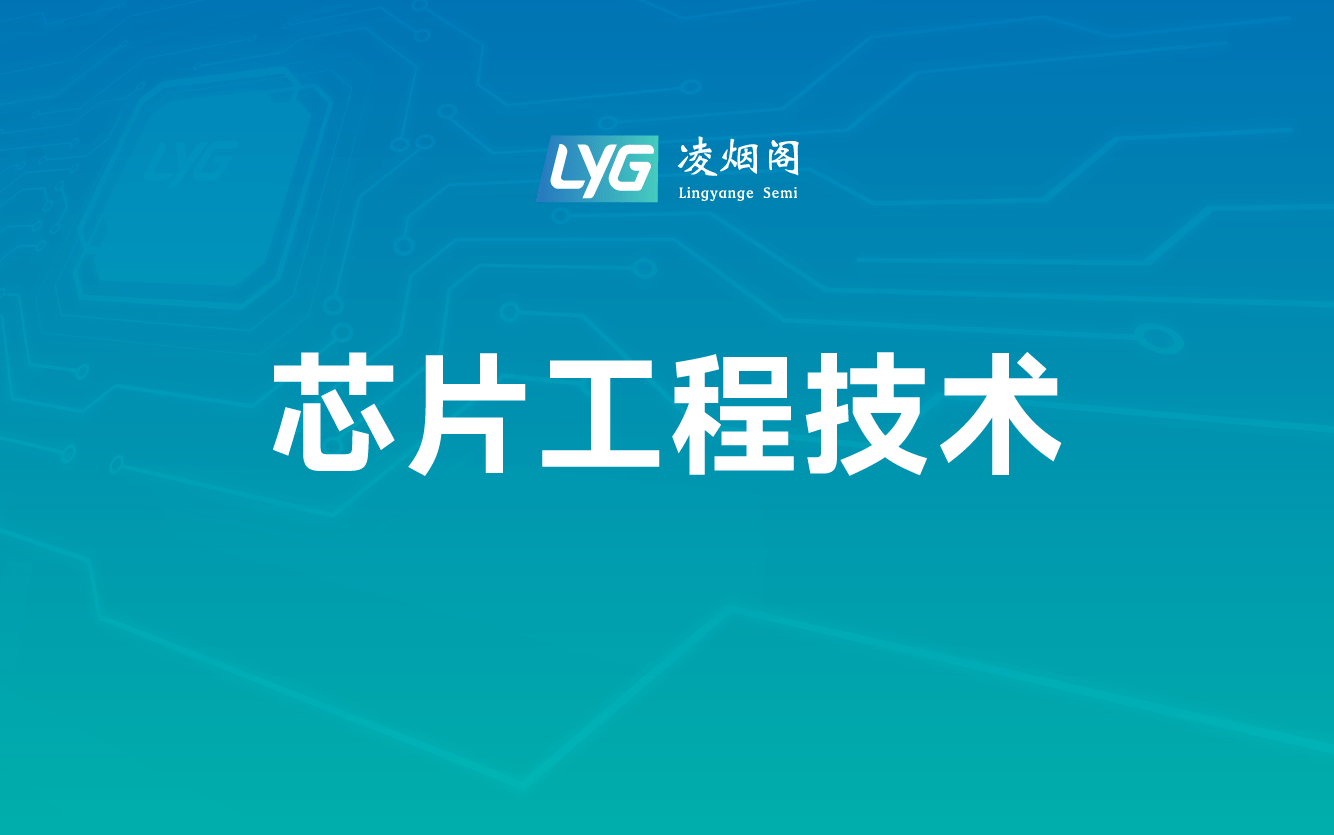
LYG has an excellent engineering team, professional wafer wafer manufacturing, a full range of packaging and testing technical support, get quality products. Lingyange assist customers from product design , tape out,product verification, package design, test program development, vehicle gauge grade verification, until the successful launch of mass production, can provide complete analysis and monitoring service. Reduce the risk of abnormal product failure.
1.Type Out Engineering and Mass Production Services:
Relying on long-term cooperation with mainstream wafer foundries at home and abroad, to provide customers with one-stop chip flow services, with efficient operational procurement and bargaining power, reduce customer costs and shorten the research and development cycle, can provide Si process (covering 0.35um-6nm) and SiC process related information and services. Proactive data checking and validation to ensure 100% accuracy, including multiple streams such as MPW, MLM, Combo and Full mask.
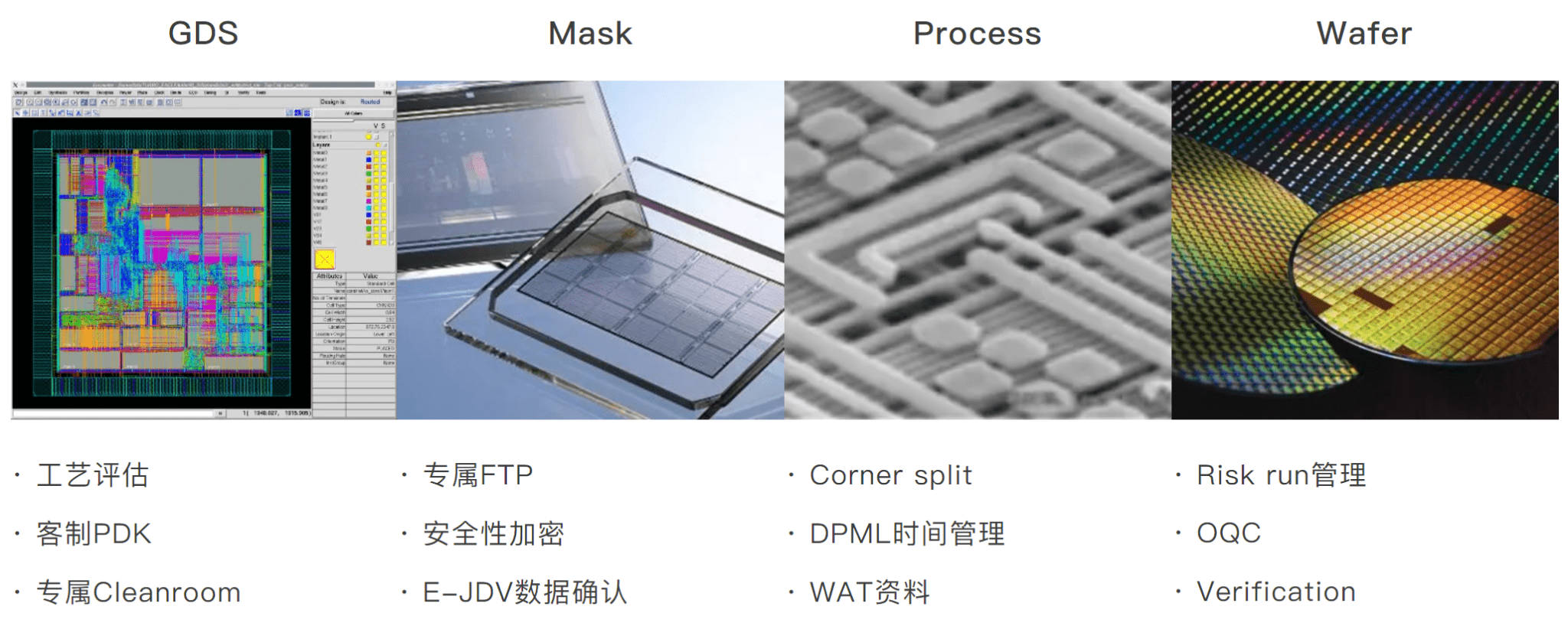
2.Product Engineering Skills:
In the wafer process, the use of rich fab equipment and integration experience, through the fab cooperation for yield analysis and improvement,
In terms of engineering support for the type out , the establishment of a base line with production characterization would reduce the risk of production enhancement. Corner lot segmentation would emphasize the worst-case process extremes that could be observed in the process of production volume. Production Data Analysis System PDAS(Production Data Analysis System) is used for production management, and WAT/PCM and CPSTDF data correlation analysis is used to improve yield and production.
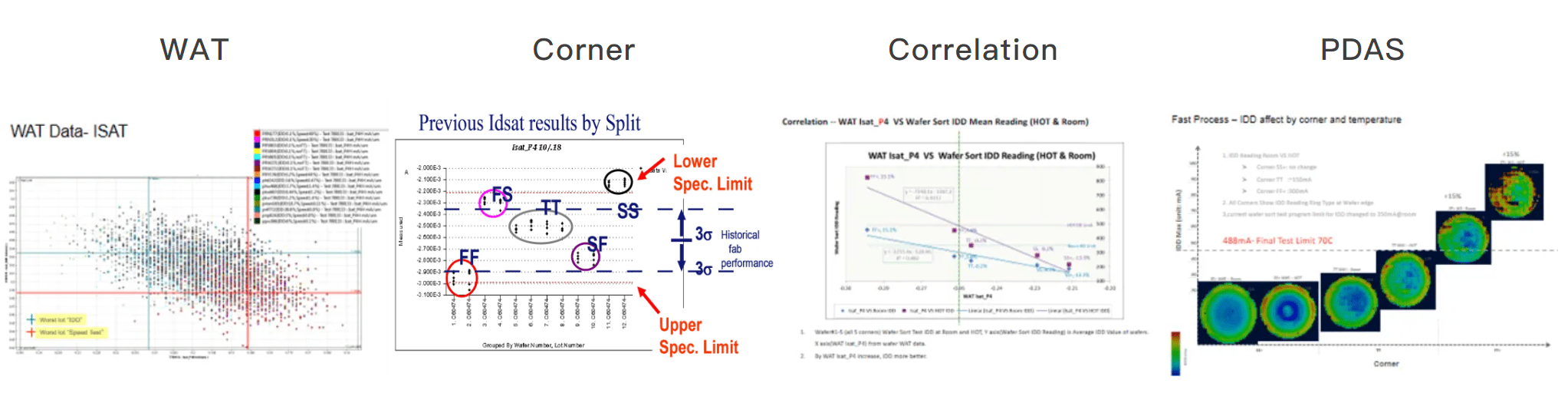
- Assist customers with Tape Out import operations
- Collect and analyze production measurement data, make yield improvement plan, and feed back to the fab and sealed test plant for yield improvement
- Establish a baseline of product characteristics to monitor production conditions and reduce the risk of product anomalies
- Develop a Corner split lot plan to verify product characteristics under extreme process conditions
- Assist customers in product failure analysis, identify product weaknesses, and develop reinforcement plans
3. Advanced Package Design:
A variety of packaging solutions are available. From the packaging technology, covering traditional wire packaging, mature core flip, to advanced such as wafer level, system level packaging. From the packaging form, the comprehensive packaging form such as QFP, QFN, BGA, WLCSP, etc., to meet the different application needs of customers. From the packaging materials, we have a variety of options to match the high reliability, low cost, short cycle and other customized needs.
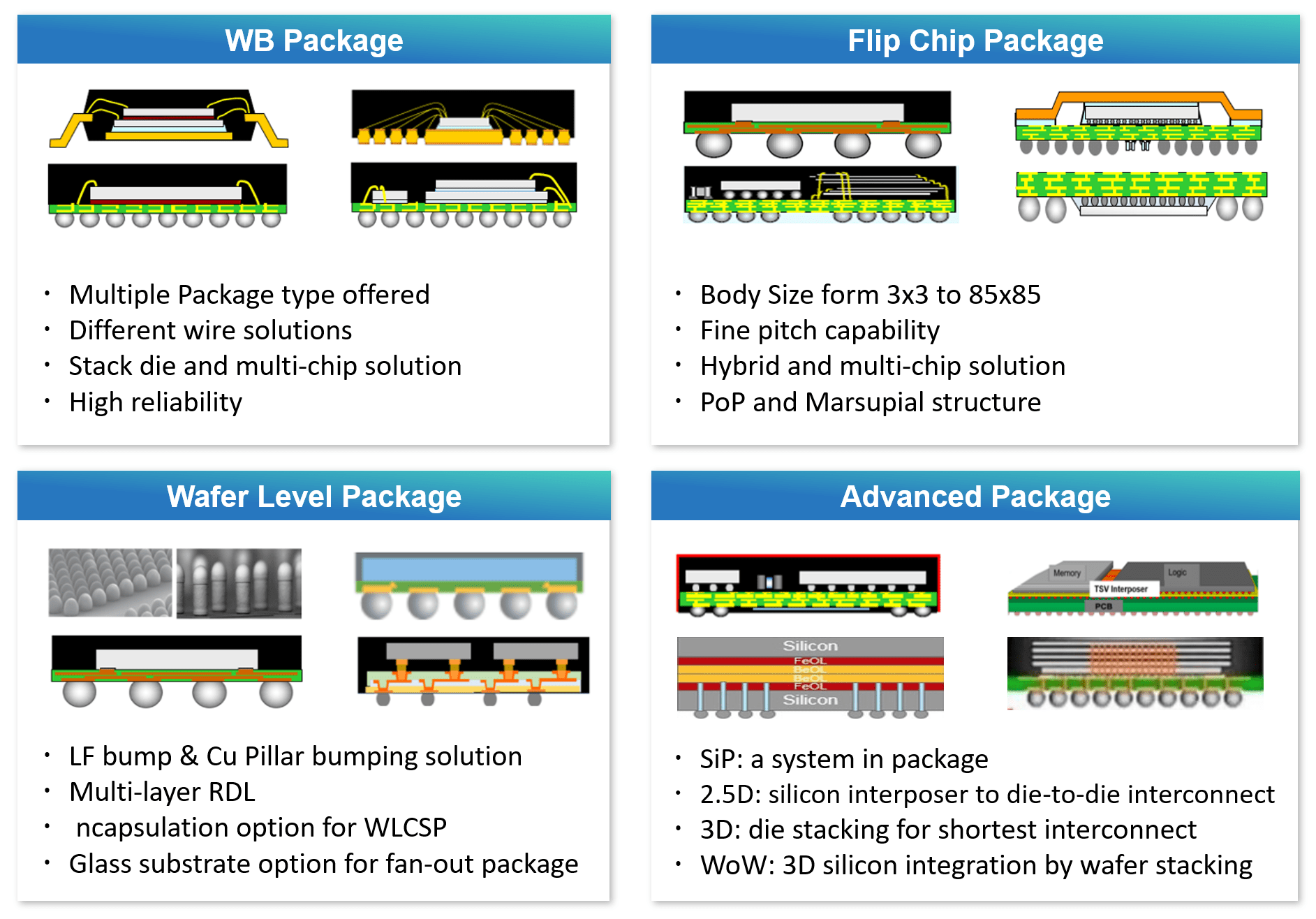
Provide not only layout design, package scheme selection, electrical/thermal/mechanical simulation, material selection, production process matching, etc., are part of our package design. The simultaneous joint design of circuit layout, simulation and production process selection is our guarantee of delivering high performance, affordable and reliable packaged products.
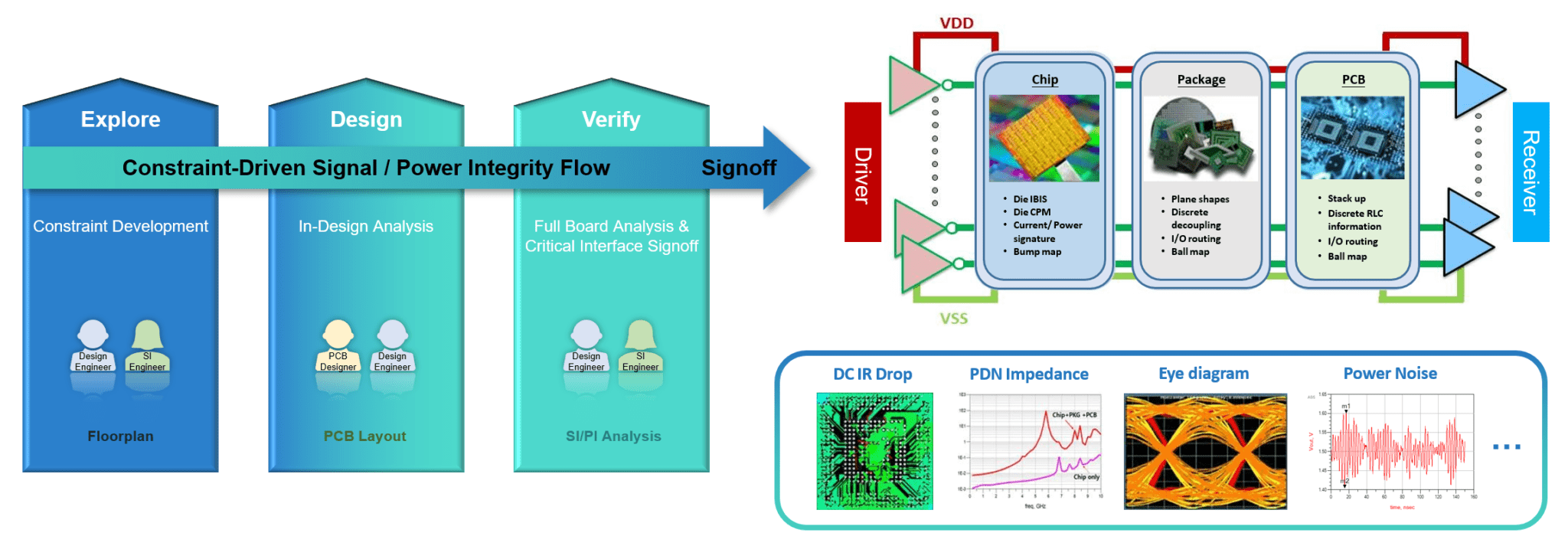
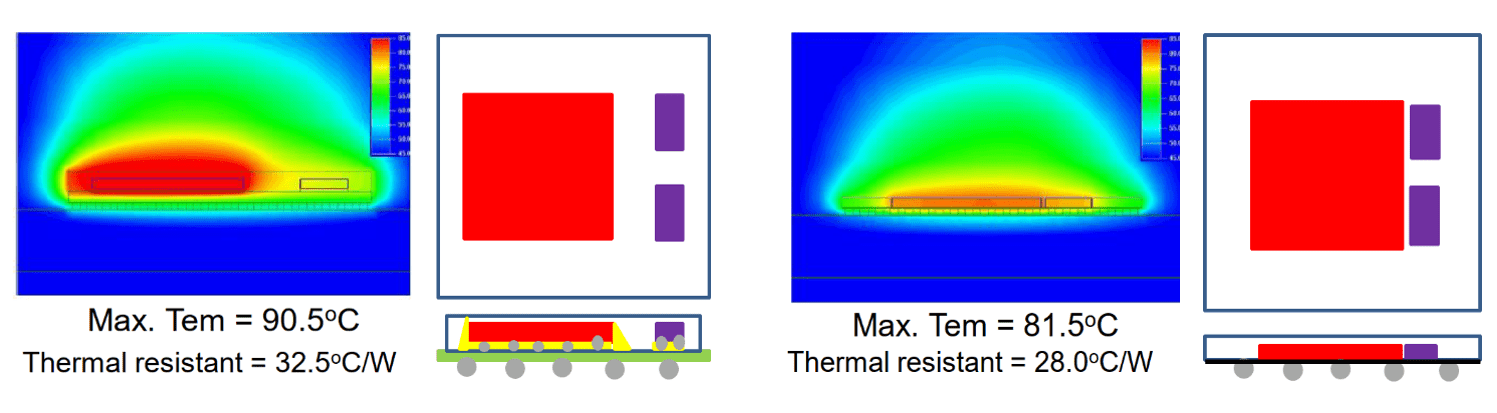
From the early feasibility assessment of the package solution to the final mass production, we follow 5 steps to ensure the delivery of stable and reliable products. Product performance, cost, delivery, reliability, productivity and other issues are evaluated in each of these steps. After the risks of the manufacturing process have been fully assessed, improvement measures are applied to ensure the smooth development of the packaged product.
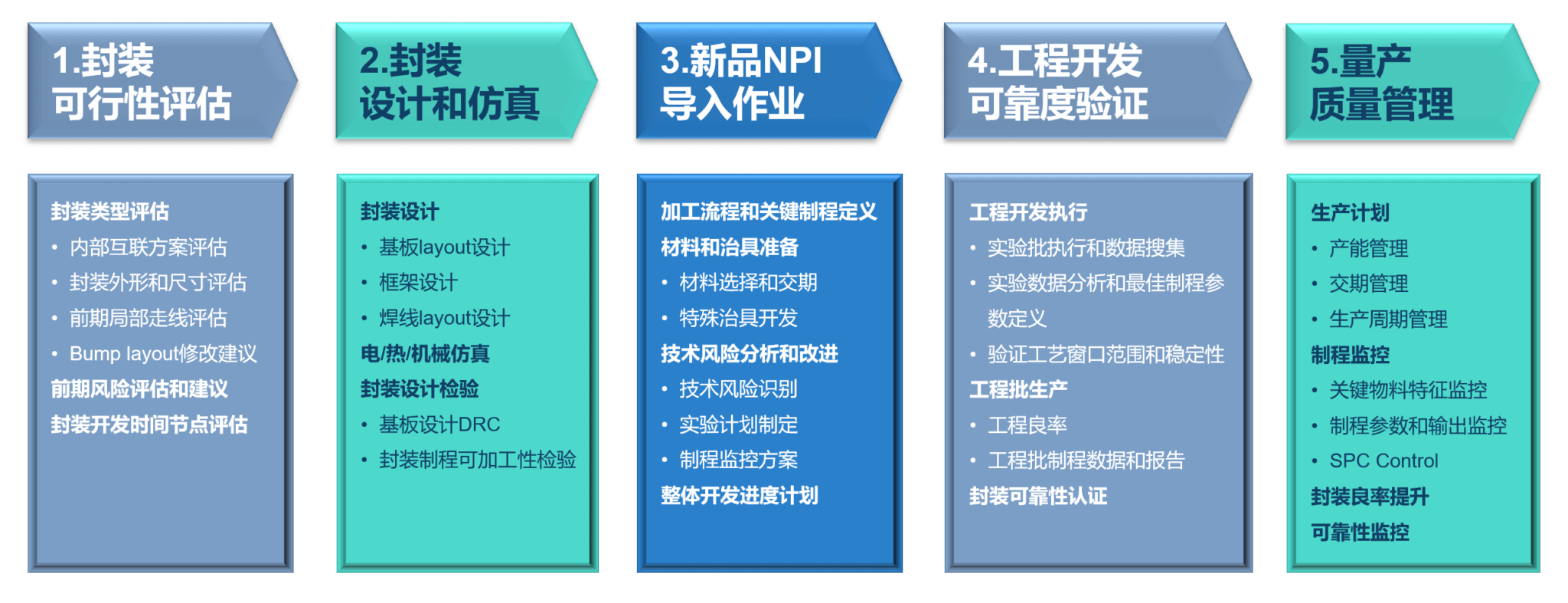
4.Test software and hardware development:
provides one-stop test development and mass production management services, including wafer (CP), finished product (FT), system (SLT) and Burn-in test program development, test accessories design and production management. LYG Testing has the support of senior technical staff with different product type development experience to provide complete and reasonable test solutions.
Follow a five-step process to ensure stable and reliable product delivery. Product performance, cost, delivery, reliability, productivity and other issues are evaluated in each of these steps to provide improvements to ensure smooth development of the packaged product.
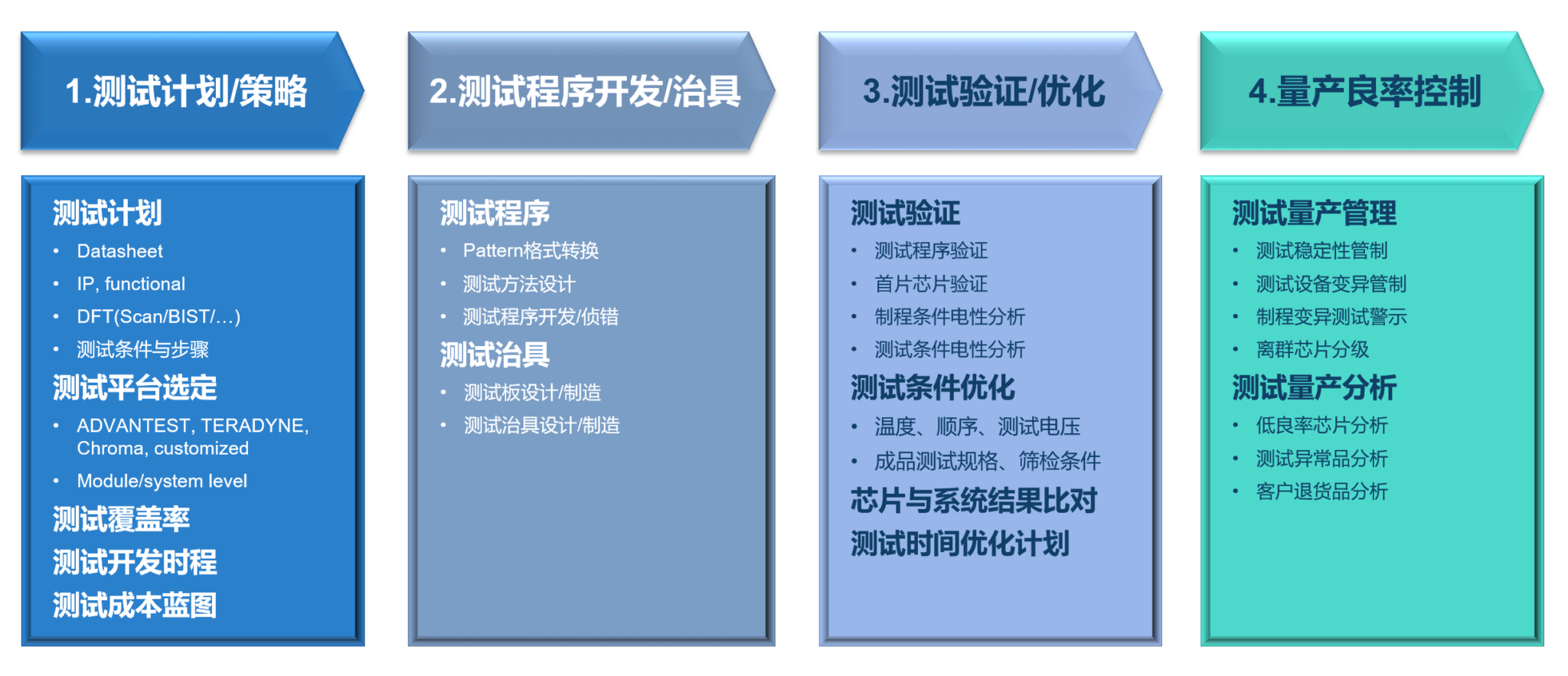
- Test machine and board::
According to customer product characteristics, V93K, UltraFLEX, J750, Chroma 3650, STS8200, CAT8280... The corresponding test platform planning, development, to meet the customer's comprehensive quality, cost, efficiency needs. According to the product characteristics, with appropriate test board resources, to help customers achieve reasonable production costs.
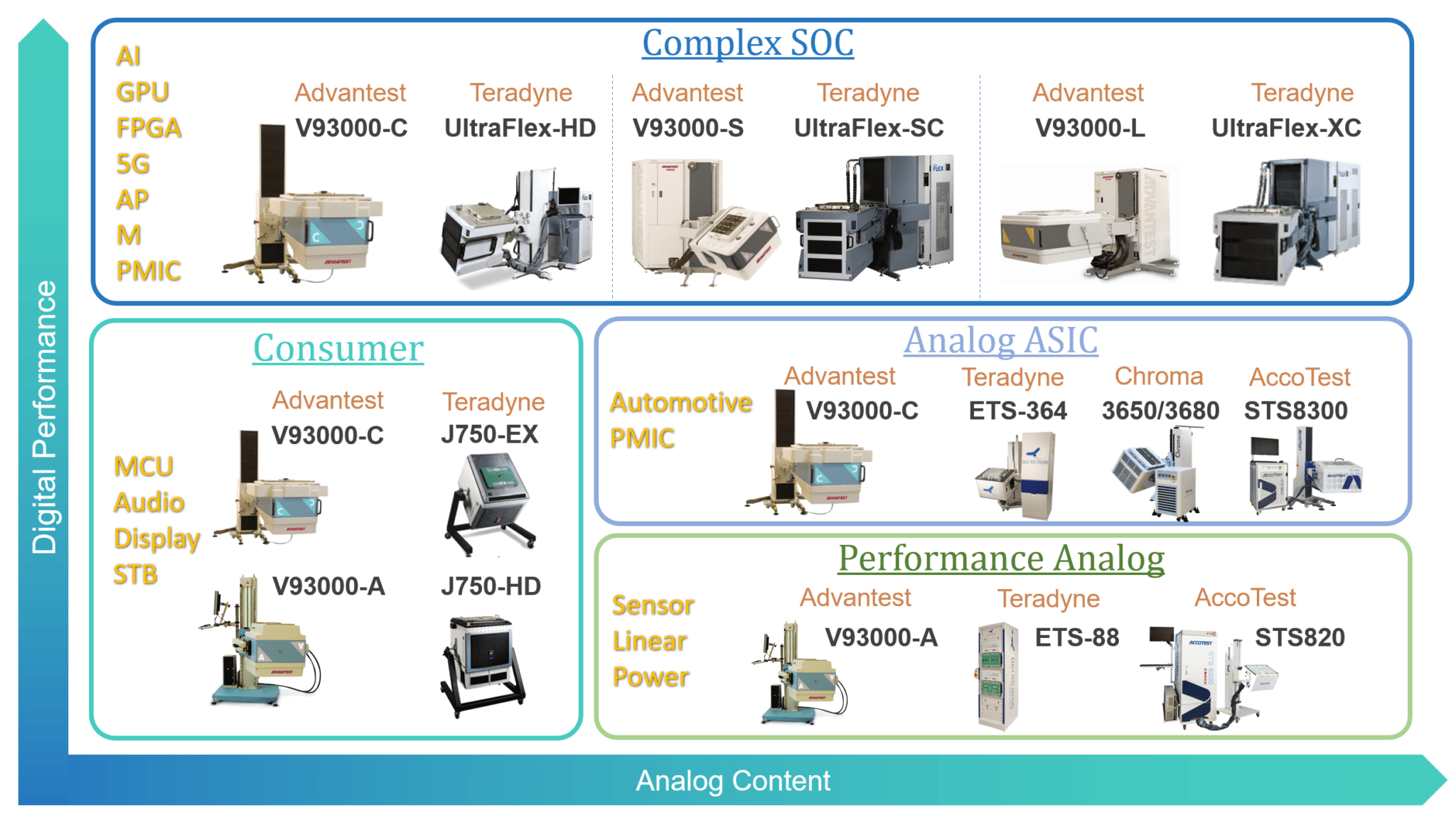
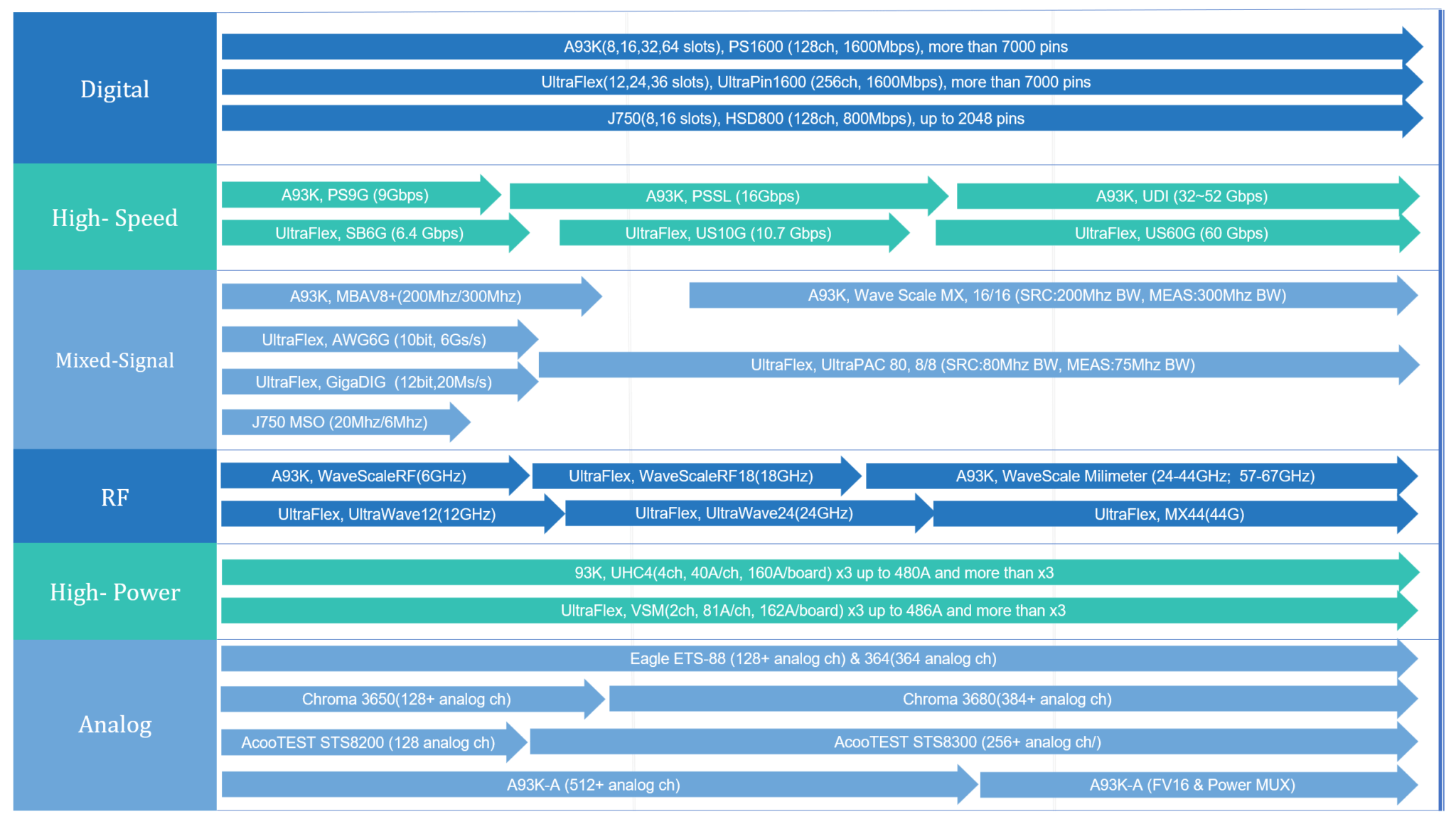
- Test Fixture
Lingyange provides the design and production management of Probe Card, Load Board, Burn-in Board, Socket and Change Kit.
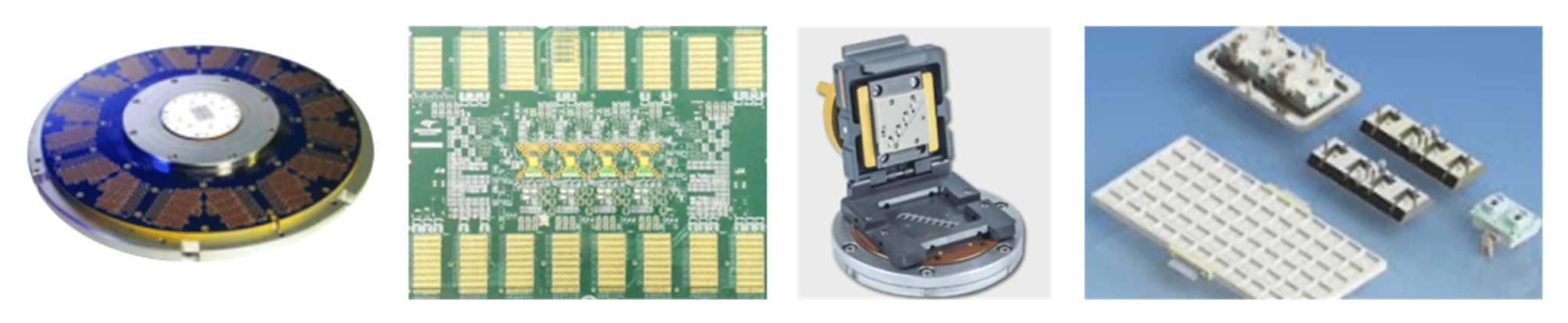
- Test Program Development:
In the chip design time, it can provide real-time chip Test testability evaluation, in the chip engineering stage, provide functional verification test development solutions, in the chip mass production stage, provide complete CP, FT, SLT and Burn-in test development solutions, and collect and analyze test data in small batch engineering testing and mass production. In order to achieve the yield target and shorten the test time, the chip reliability laboratory provides an overall test and verification solution.
Provide small batch production of chips, provide to import other cooperative closed test factories for large-scale production, can provide conversion between different test platforms, to meet the needs of customers for optimal mass production purposes.
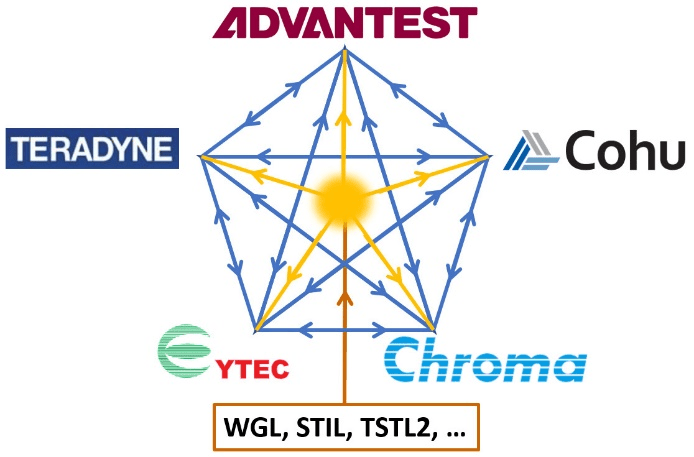
- Support WGL, STIL, TSTL2 pattern format development
- Supports pattern conversion among test platforms
- IIC、UART、JTAG、SWD…Communication port format test program development
- Custom communication port format program development
- OTP(One Time Program ) test program development
- Characteristics Analysis:
According to the chip design specifications, formulate and plan the characteristic analysis during the Production Validation Test (PVT), and develop the test program dedicated to the characteristic analysis. Define Junction temperature and Corner lot to collect product characteristic measurement data, conduct detailed analysis, review product characteristic distribution, review Yield results, and develop improvement plans.
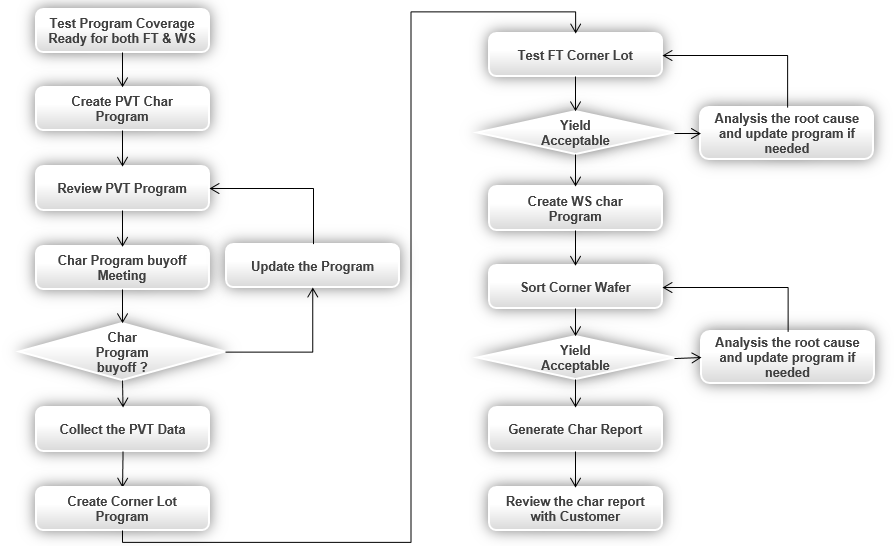

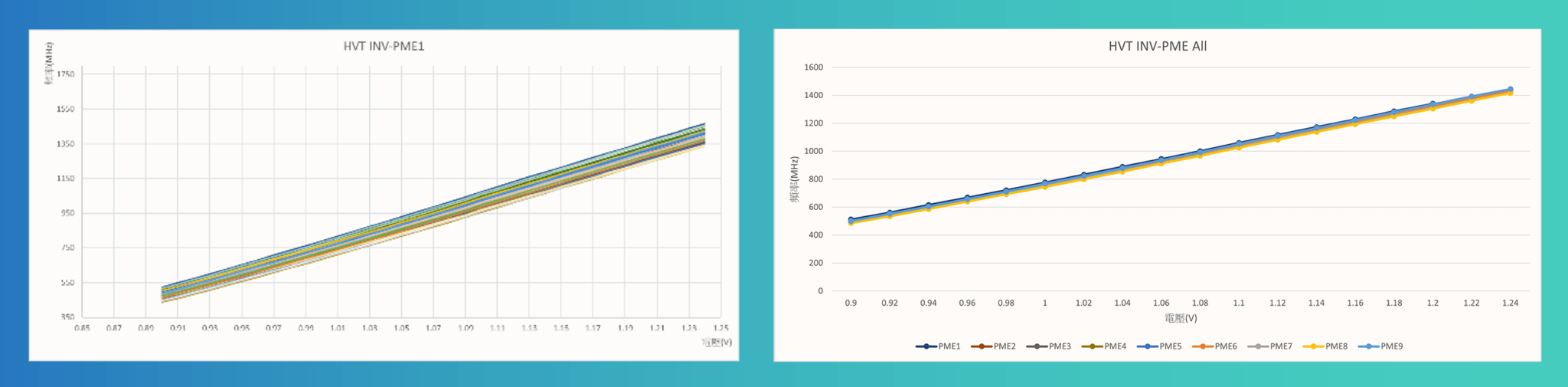
5.Vehicle regulation verification solution:
The testing process of automotive chips is much more rigorous than that of ordinary consumer chips, which must undergo three-temperature CP testing, remove Outlier grains through GPAT, screen suitable wafers through SYL/SBL mechanism for packaging, and then remove Outlier chips through three-temperature FT testing with SPAT/GPAT mechanism. Burn-In tests are designed to weed out abnormal products that die early; SLT can make up for system-level testing that FT cannot cover.
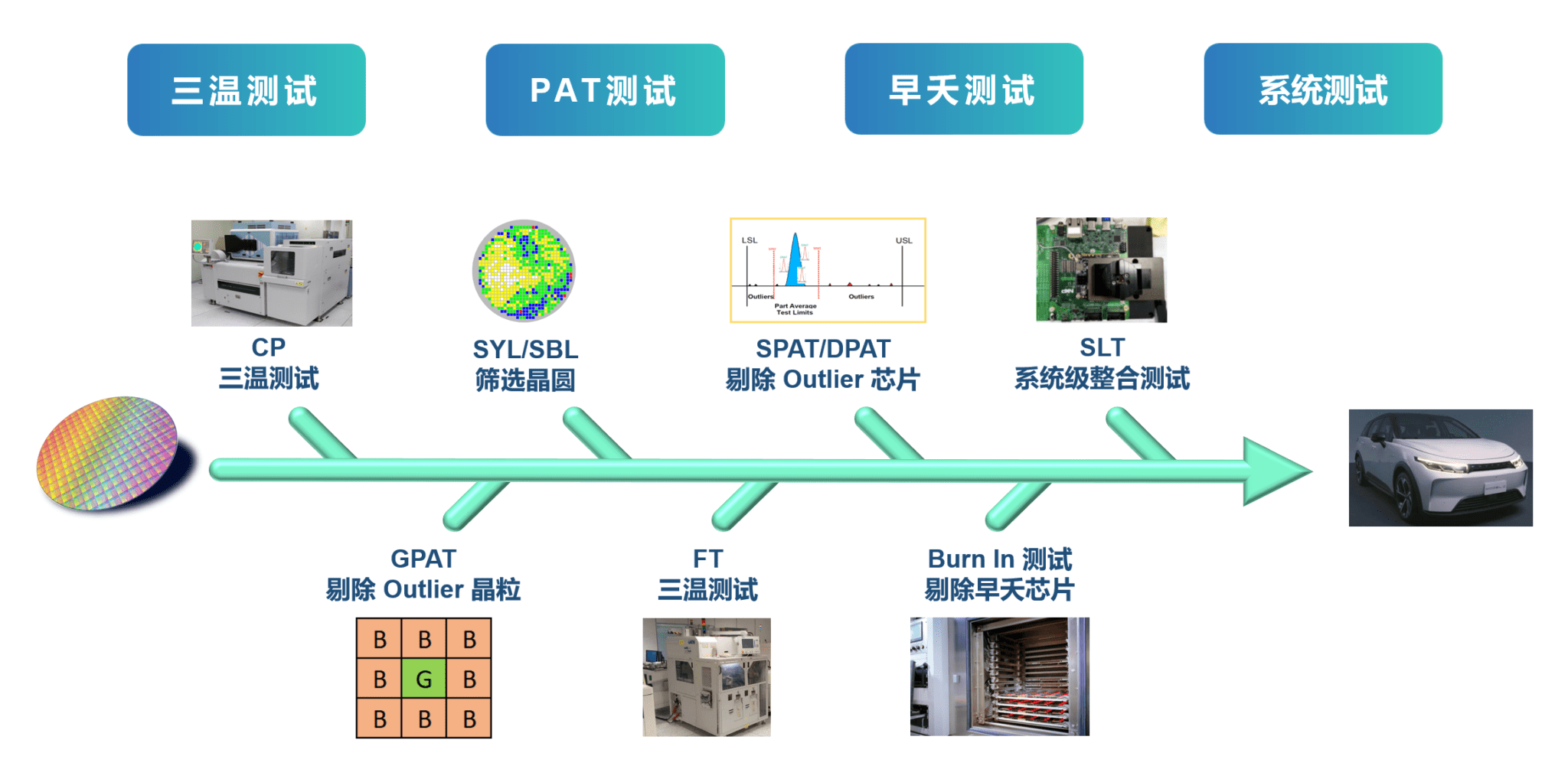
LYG checks for customers with rigorous testing process, and produces the highest quality automotive level chips.